4 Wichtige Verbrauchsmaterialien für das Lichtbogenschweißen
Dieser Artikel beleuchtet die vier wichtigen Verbrauchsmaterialien des Lichtbogenschweißens. Die Verbrauchsmaterialien sind: - 1. beschichtete Elektroden 2. Schweißstäbe und -drähte 3. Schweißflussmittel 4. Schutzgase.
Verbrauchsmaterial 1. beschichtete Elektroden:
Fast alle Universalschweißungen werden durch geschirmtes Metall-Lichtbogenschweißen mit beschichteten Elektroden durchgeführt. Die beschichteten Elektroden bestehen aus dem Kerndraht mit einer Beschichtung aus Beschichtungsmaterial. Der für Elektroden verwendete Kerndraht wird nach bestimmten nationalen oder internationalen Normen hergestellt, die die Drahtstärke, Materialzusammensetzung, Abnahmeregeln usw. festlegen.
Elektroden zum manuellen und automatischen Lichtbogenschweißen von Stählen mit niedrigem und mittlerem Kohlenstoffgehalt sowie niedriglegierten Stählen werden meistens aus 012% Kohlenstoffstahl hergestellt.
Der Kerndrahtdurchmesser für Elektroden variiert normalerweise zwischen 3, 15 und 12, 50 mm, wobei der Standarddurchmesser 4, 00, 5, 00, 6, 30, 8, 00 und 10, 00 mm beträgt. Die Länge dieser beschichteten Elektroden variiert zwischen 350 und 450 mm, wobei der bloße Bereich (ohne Beschichtung) zwischen 20 und 30 mm liegt, von denen er in einem Elektrodenhalter gehalten wird.
Die chemischen Zusammensetzungen von Kerndrähten für Stähle mit niedrigem und mittlerem Kohlenstoffgehalt sind in Tabelle 5.1A und für Weichstahl-Elektrodenkerndrähte in Tabelle 5.1B angegeben:


Verbrauchsmaterial Nr. 2. Schweißstäbe und -drähte:
Nackte Schweißdrähte und -stäbe werden in kurzen Längen von etwa 1 Meter oder in Spulenform verwendet. Während kurze Längen für Prozesse wie das WIG und das Plasmaschweißen verwendet werden, bei denen sie nicht Teil des Schweißkreislaufs sind, werden lange Drähte für Prozesse wie GMAW und SAW verwendet, bei denen ein Teil des Drahtes Strom leitet, wenn ein Schweißdraht einen Teil des Schweißdrahtes bildet Elektrische Schaltung wird als Schweißelektrode bezeichnet, ansonsten als Schweißstab.
Die meisten Drähte, die zum Schweißen von Baustahl verwendet werden, enthalten normalerweise 0-10% Kohlenstoff und 0-35 bis 0-60% Mangan. Andere haben den Mangangehalt erhöht. Einige andere Typen haben erhöhte Mengen an Kohlenstoff, Mangan und Silizium.
Überschüssiges Silizium im Schweißdraht führt zu starkem Spritzen, zur Gasung im Schweißbad und zu nichtmetallischen Materialien im Schweißgut. Der maximal zulässige Siliziumgehalt beträgt daher bis zu 0-95%.
Der Gehalt an schädlichen Verunreinigungen wie Schwefel und Phosphor sollte jeweils 0 - 04% nicht überschreiten. Bei einigen Drähten, insbesondere beim Schweißen von Legierungsstählen, beträgt die maximal zulässige Menge an Schwefel und Phosphor jeweils 0 bis 3%.
Der Bereich des Drahtdurchmessers reicht von 0-5 bis 2-5 mm mit 0-5, 0-6, 0-8, 0-9, 1-0, 1-2, 1-6, 2-0, 2- Normalerweise sind Drähte mit Durchmessern von 4 und 2-5 mm erhältlich. Schweißmaschinen verwenden Endlosdrähte in Spulen. Abhängig vom Drahtdurchmesser kann eine Spule zwischen 5 und 500 kg wiegen und einen Durchmesser von 150 bis 1000 mm haben.
Die Schweißdrähte sind normalerweise mit Kupfer beschichtet, um Rostbildung zu verhindern und die Stromaufnahme aus dem Kontaktrohr zu verbessern. Dies hilft auch beim Ziehen von Drähten durch Matrizen. Um schädliche Einflüsse und ein Abschälen der Kupferschicht zu vermeiden, wird sie normalerweise sehr dünn gehalten und die maximale Kupfermenge wird mit 0 bis 4 Gew .-% des Drahtes angegeben.
Neben kohlenstoffarmen Stählen werden Schweißdrähte auch aus nichtrostenden Stählen, Aluminium und seinen Legierungen, Nickellegierungen, Magnesiumlegierungen, Titanlegierungen und Kupferlegierungen hergestellt.
Die Schweißdrähte sind sowohl in fester als auch in rohrförmiger Form erhältlich, wobei letztere Flussmittel enthält.
Spezifikationen für feste Drähte und Stäbe :
Mehrere Systeme werden verwendet, um Schweißelektroden oder -stäbe festzulegen. Die AWS-Spezifikation ist eines der bekannten Kodifizierungssysteme. Es besteht aus einem Präfixbuchstaben oder -buchstaben, gefolgt von zwei Ziffern und dem Buchstaben S und dann einem Suffix, bei dem es sich um eine Zahl oder einen Buchstaben oder um beides handeln kann.

Die AWS-Kennzeichnung für blanke Kohlenstoffstahl-Elektroden und -Stäbe für das Schutzgasschweißen lässt sich anhand des Codes ER-70S-1 erklären
ER - Präfix bezeichnet eine Elektrode oder einen Schweißstab
70 - zeigt eine Mindestzugfestigkeit im geschweißten Zustand von 5000 N / mm 2 (70.000 psi).
S - bedeutet feste Elektrode oder Stab
1 …… .. 6— Die Suffixzahl gibt die chemische Analyse oder einen anderen Verwendbarkeitsfaktor an, z. B. 1 zeigt 0 bis 07% Kohlenstoff und 0 bis 30% Silizium.
Alle diese Drähte und Stäbe sind normalerweise für die Verwendung mit tiefer Polarität gedacht und die meisten von ihnen sind für die Verwendung von CO 2 als Schutzgas ausgelegt.
Das AWS-System, das zum Identifizieren von massiven blanken Kohlenstoffstahldrähten für das Unterpulverschweißen verwendet wird, lautet wie folgt:
Es hat einen Präfixbuchstaben E, um eine Elektrode anzuzeigen. Darauf folgt ein Buchstabe L oder M oder H, um den Gehalt an Mangan anzuzeigen. L steht für niedrig, M für mittel und H für hohen Mangangehalt. Es folgen eine oder zwei Zahlen, um die durchschnittliche Kohlenstoffmenge in Hundertstel Prozent darzustellen, zum Beispiel bedeutet 8 0, 08% Kohlenstoff. Das Suffixbuchstabe K wird verwendet, um den Siliziumgehalt höher als 0 05% anzuzeigen.
Beispiele :
EL8 - Manganarm (0-30 - 0-55%), durchschnittlicher Kohlenstoffgehalt 0 - 08%, 0 - 05% Silizium
EL8K - (0-30-0-55)% Mn, 0-08% C, (0-10-0-20)% Si
EM12 - (0-85 - 1-25%) Mn, (0-09 - 0-15)% C, 0-05% Si
EH 14 - (1-75-2-25)% Mn, (0-10-0-18)% C, 0-05% Si
Einige dieser Drähte sind in ihrer Zusammensetzung denjenigen ähnlich, die für das Gasmetall-Lichtbogenschweißen verwendet werden.
Rohrelektroden oder flussmittelgefüllte Drähte:
Der Fülldraht besteht aus einem Metallmantel, der einen Flussmittelkern umgibt. Das in der Elektrode enthaltene Flussmittel erfüllt im Wesentlichen die gleichen Funktionen wie die Beschichtung auf einer bedeckten Elektrode, d. H. Es wirkt als Desoxidationsmittel, Schlackenbildner und Lichtbogenstabilisator und kann Legierungselemente sowie das Schutzgas bereitstellen.
Es gibt zwei Hauptgründe für die Einführung von Fülldraht, nämlich im Gegensatz zu Massivdraht, der nicht notwendigerweise Stahlbarren einer bestimmten Zusammensetzung für seine Herstellung benötigt, da er aus Streifen des gewünschten Materials hergestellt werden kann; Es ist auch einfacher zu verwenden, insbesondere zum Schweißen von fest verlegten Rohren.
In der jetzigen Form wurden gefluxte Drähte 1956 in den USA eingeführt. Zuerst wurde das Band mit dem Flussmittel durch Falten auf den erforderlichen Durchmesser gebracht, aber spätere Entwicklungen führten zu einem nahtlosen Metallrohr um den Kern, der das Flussmittel enthält. Es gibt verschiedene Fülldrähte unterschiedlicher Konfiguration, von denen einige in Abb. 5.1 dargestellt sind.

Anfangs wurden Fülldrähte mit einem Durchmesser von 3, 2 mm hergestellt, jetzt sind sie bis zu einem Durchmesser von 11 mm erhältlich.
Typische Fülldrähte werden mit CO 2 als Schutzgas verwendet, wobei Flussmittel die schlackebildenden Bestandteile und Legierungselemente enthält. In vielen Fällen enthalten die Drähte auch Eisenpulver, eingelegte Drähte oder Metallstreifen, die teilweise leitfähig sind.
Der Drahtdurchmesser liegt normalerweise im Bereich von 1-2 bis 4 mm, wobei der Fluss normalerweise 5 bis 25 Gew .-% des gesamten Drahtes ausmacht, was zu einer Abscheidungseffizienz von 85 bis 95% führt.
Arten von Fülldrähten:
Die meisten der zum Schweißen von Kohlenstoffstählen verfügbaren Fülldrähte sind vom Rutiltyp, wobei TiO 2 (Titandioxid) der Hauptbestandteil der Schlacke ist. Diese Drähte ermöglichen ein relativ spritzerfreies Schweißen und erzeugen Schweißnähte mit glatter Oberfläche und leicht entfernbarer Schlacke.
Beliebtere sind jedoch Fülldrähte des Basistyps. Die schlackebildenden Bestandteile dieser Drähte sind Calciumfluorid, Kalkstein, Erdalkalimetallcarbonate und -oxide. Bei niedrigen Strömen erzeugen diese Drähte mehr Spritzer, bei höheren Strömen ist die Metallübertragung jedoch glatt und weist nur wenig Spritzer auf. Bei Kohlenstoffstählen ergeben die Grunddrähte Schweißnähte mit einer besseren Schlagfestigkeit als Rutilelektroden. Ein weiteres auffälliges Merkmal des Schweißgutes, das unter Verwendung von Basis-Fülldrähten erhalten wird, ist seine Unempfindlichkeit gegenüber Spannungsarmglühen. Nach dem Tempern bei etwa 600 ° C findet der gefürchtete Abfall der Schlagfestigkeit nicht statt.
Während der Wasserstoffgehalt des Schweißguts in basisch umhüllten Elektroden selbst bei vollständiger Trocknung vor der Verwendung 3 ml / 100 g Schweißgut beträgt, kann es für das Flussmittel nur 1-2 ml / 100 g Schweißgut sein. Fülldrähte.
Es gibt zwei Hauptarten von Fülldrahtelektrodenleitungen, nämlich Einzel- und Mehrfachdrähte. Ersteres ergibt einen relativ hohen Gehalt an Mangan und Silizium im Schweißgut als letzteres. Die Fülldrähte können auch gasgeschirmt oder selbstgeschirmt sein (keine äußere Gasabschirmung), d. H. Sie werden durch Gas abgeschirmt, das durch Zersetzung und Verdampfung des Flusskerns erzeugt wird. Im letzteren Fall schirmt die geschmolzene Schlacke das Tröpfchen während der Metallübertragung ab.
CO 2 -geschirmte und selbstgeschirmte Fülldrähte werden in zunehmendem Maße hauptsächlich zum Schweißen von Stahl mit einer Dicke von mehr als 12 mm verwendet, wobei ihre Hauptattraktion die Fähigkeit ist, Metall unter Verwendung halbautomatischer Schweißsysteme kontinuierlich und sehr schnell abzuscheiden. Die Verwendung von GMAW mit Argon-reichen Gasgemischen für Schweißstähle, hauptsächlich mit einer Dicke von weniger als 12 mm, wuchs gleichzeitig. Der Hauptvorteil davon war die Kombination aus hoher Schweißgeschwindigkeit mit gutem Finish und minimalem Spritzer und Schlacke.
Das Kodiersystem zum Identifizieren von Fülldrähten folgt dem gleichen Muster wie das für GMAW-Massivdrähte, ist jedoch für rohrförmige Elektroden spezifisch.
Nehmen Sie zum Beispiel E60T - 7
Hier,
E - Zeigt eine Elektrode an.
60 - Gibt die minimale Zugfestigkeit von 420 N / mm (60.000 psi) an.
T - Weist auf eine röhrenförmige, gefertigte Elektrode oder eine Elektrode mit Flussmittelkern hin.
7 - Eine Zahl zwischen 1 und 8 als Suffix gibt die Chemie des abgelagerten Schweißgutes, des Schutzgases und des Verwendbarkeitsfaktors an.
Zu den bekannteren Spezifikationen gehören der Rutil-Typ (E70T-1 und E70T-2), der selbstgeschirmte Typ (E70T-4) und der Basistyp (E70T-5).
Neben Kohlenstoffstahl-Basis-Fülldrähten wurden auch niedriglegierte Stahl-Fülldrähte entwickelt, die es ermöglichen, Schweißgut herzustellen, das für die meisten Stahlsorten und für unterschiedliche technische Anforderungen geeignet ist. Mit Nickel, Molybdän und Chrom legierte geflechte Drähte können zum Schweißen hochfeiner feinkörniger Baustähle verwendet werden, die bisher mit basisch beschichteten Elektroden und Grundflüssen verschweißt werden sollten.
Die Fülldrahttechnologie hat die Benutzer dazu veranlasst, vom Festdraht-CO 2 -Prozess auf den Fülldrahtprozess umzusteigen, um verschiedene Vorteile zu erzielen. Das Verfahren ist wesentlich schneller, einfacher und wirtschaftlicher als das Unterpulverschweißen. Bei bestimmten Anwendungen, z. B. im Schiffbau, wird eine höhere Produktivität erzielt. Rohr- oder Fülldrähte werden auch für Oberflächen- und SAW-Anwendungen eingesetzt.
Ein Fülldraht, in dem Flussmittel durch Metallpulver ersetzt wurde, wird mit argonreichem Schutzgas verwendet, um Schweißgut mit sehr hohen Geschwindigkeiten in Stahlplatten mit einer Dicke von 5 bis 60 mm abzuscheiden. Sie haben gute mechanische Eigenschaften, sind nahezu spritzerfrei und schlackenarm. Rauch ist auch gering und Schlackenentfernung zwischen den Durchläufen ist nicht notwendig.
Das MIG-Schweißen mit Fülldraht vereint die besten Eigenschaften der Inertgasabschirmung und der Fülldrahttechnologie. Der Massivdraht wird durch einen Fülldraht ersetzt, bei dem der Kern aus Metallpulvern und Desoxidationsmitteln anstelle der normalen Schlackebildenden Flüsse besteht. Wenn dieser Draht unter einem Schutzgas aus Argon mit einem geringen Prozentsatz an CO 2 -Schweißnähten abgeschieden wird, sind die Schweißnähte praktisch identisch mit den MIG-Schweißnähten, jedoch mit höheren Ablagerungsraten, die mit den Fülldrähten verbunden sind.
Die Fülldrähte werden normalerweise mit einem Durchmesser von 1, 6 mm hergestellt und sind für das Schweißen an allen Positionen mit einem höheren prozentualen Rückstellwert ausgelegt, wenn sie mit argonreichem Gas verwendet werden, und es gibt praktisch keine Schlacke. Die prozentuale Rückgewinnung, die als Verhältnis des Gewichts des abgelagerten Metalls zum Gewicht der verwendeten Verbrauchsstoffe, multipliziert mit 100, definiert ist, variiert von Prozess zu Prozess, wie in Tabelle 5.3 dargestellt.

Verbrauchsmaterial Nr. 3: Schweißflussmittel:
Flussmittel sind ein wesentlicher Aspekt des Unterpulverschweißens und dienen folgenden Zwecken:
1 Der Teil des Flussmittels, der schmilzt wie eine flüssige Decke über dem geschmolzenen Metall, schützt es vor den schädlichen Einflüssen der umgebenden Atmosphäre, wodurch die Aufnahme von Sauerstoff und Stickstoff verringert wird.
Eine Vorstellung von der Wirksamkeit eines Flussmittels zum Schutz des Schweißbades vor atmosphärischer Verunreinigung kann aus dem Stickstoffgehalt des Schweißgutes gewonnen werden. Beim Schweißen mit blanken Elektroden beträgt der Stickstoffgehalt des Schweißgutes 0 - 18%. Schwere beschichtete Elektroden halten die Zahl auf 0-026%, während in SAW maximal 0 005% Stickstoff in der Schweißnaht enthalten sind.
Es wirkt als guter Isolator und konzentriert die Wärme in einer relativ kleinen Schweißzone, wodurch das Schmelzen des geschmolzenen Metalls von der Schweißelektrode und dem Grundmaterial verbessert wird.
3. Es reinigt das Schweißgut, absorbiert Verunreinigungen und fügt Legierungselemente wie Mangan und Silizium hinzu.
4. Aufgrund des Flussmittels ist das Schweißgut nicht nur sauber, sondern auch dichter und weist daher hervorragende physikalische Eigenschaften auf.
5. Die Flussmitteldecke verbessert die Prozesseffizienz, indem Spritzer- und Verbrennungsverluste reduziert werden, die bei einem normalen offenen Lichtbogen nicht zu vermeiden sind.
Zusammensetzung und chemische Klassifizierung von SAW-Flussmitteln:
Die Bestandteile von Flussmitteln sind im Wesentlichen Rohstoffe geologischen Ursprungs, die auf Kieselsäure, Silikaten, Kalkstein, Ton, Oxiden, Fluoriden und anderen Mineralien basieren. Viele Bestandteile eines Flussmittels verbessern seine Eigenschaften nicht wesentlich, sondern liegen hauptsächlich als Rückstand vor; Bis zu einem gewissen Grad können sie jedoch sein physikalisches und chemisches Verhalten beeinflussen.
Im Allgemeinen besteht ein SAW-Fluss aus Quarz (SiO 2 ), Hausmanile (Mn 3 O 4 ), Korund (Al 2 O 3 ), Periklas (MgO), Calcit (CaCO 3 ), Fluorit (CaF 2 ), Kalkstein (CaO). Zirkonoxid (ZrO 2 ), Kryolith (Na 3 AlF 6 ), Dolomit (CaMg (CO 3 ) 2 ), Ferrosilicium (FeSi 2 ), Magnesit (MgCO 3 ), Rhodenit (MnSi0 3 ), Rutil (TiO 2 ), Wellastonit (CaSiO 3 ), Zirkon (ZrSiO 4 ) sowie Oxide von Barium, Natrium, Kalium und Eisen, dh BaO, Na 2 O, K 2 O und FeO. Sie kann aus all diesen Elementen oder einigen davon in den gewünschten Anteilen bestehen. Jedes Element bewirkt unterschiedliche Eigenschaften des Schweißflusses, so dass die Manipulation seiner Proportionen die Eignung des Flusses für die Anforderungen ermöglicht.
In Abhängigkeit von der Menge der verschiedenen Bestandteile kann ein Flussmittel sauer, basisch oder neutral sein.
Diese Eigenschaften werden durch BASICITY INDEX (BI) des Flusses bestimmt, der als Verhältnis von basischen Oxiden zu sauren Oxiden definiert ist, das heißt:


Ein Flussmittel gilt als sauer, wenn BI <1, neutral für BI zwischen 1-0 und 1-5, basisch für BI zwischen 1, 5 und 2, 5 und stark basisch für BI mehr als 2, 5.
Einige der aufgrund der obigen Überlegungen klassifizierten Flüsse sind in Tabelle 5.4 angegeben:
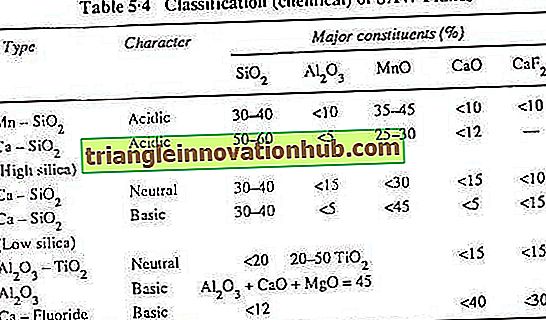
Rollen der Flussmittelbestandteile:
1. Siliciumdioxid (SiO 2 ):
Es ist ein saures Oxid, das den Hauptgradienten aller SAW-Flüsse bildet. Es verleiht dem Flussmittel im geschmolzenen Zustand die notwendige Viskosität und Strombelastbarkeit. Je höher der SiO 2 -Gehalt, desto höher die Viskosität und die Strombelastbarkeit des Flussmittels. Es verbessert die Ablösefähigkeit der Schlacke mit dem Ergebnis, dass die Schweißraupe auch bei 1000 A ohne Hinterschnitt wirkt. SiO 2 führt jedoch zum Verlust von Desoxidationsmitteln und bewirkt eine Diffusion von Silizium in das Schweißgut, was zu schlechteren mechanischen Eigenschaften, insbesondere der Schlagfestigkeit, führt.
SiO 2 im Fluss variiert von 25 bis 55 Gew .-%. Die Flussmittel, die mehr als 40% SiO 2 enthalten, zeigen jedoch eine schnelle Oxidation von Legierungselementen und erhöhte Mengen an nichtmetallischem Einschluss im Schweißgut, was zu einer verringerten Zähigkeit des Schweißgutes führt.
SiO 2 verringert das Verhältnis von Breite zu Durchdringung der Schweißnaht. Es verringert auch die Lichtbogenstabilität.
2. Manganoxid (MnO):
Dies führt dazu, dass Mangan mit dem Schweißgut legiert wird, wodurch seine Eigenschaften unter Null verbessert werden.
MnO begünstigt höhere Schweißgeschwindigkeiten und ein tieferes Eindringen. Es verringert die Empfindlichkeit gegen Rostporosität, verringert aber auch die Strombelastbarkeit und Viskosität. MnO verbessert jedoch die Lichtbogenstabilität.
3. Rutil (TiO 2 ):
Es ist chemisch neutrales Oxid. Es bietet metallurgische Vorteile durch die Bildung von nadelförmigem Ferrit aufgrund der Kornfeinung. Es verbessert die Lichtbogenstabilität und die Schlagfestigkeit.
4. Aluminiumoxid (Al 2 O 3 ):
Es verbessert auch die Schlagzähigkeitseigenschaften des Schweißgutes (Kornfeinung und Bildung von nadelförmigem Ferrit. Es verringert jedoch die Lichtbogenstabilität und -viskosität und führt zu einer mittleren Penetration.
5. Zirkoniumoxid (ZrO 2 ):
Es entfernt die schädlichen Elemente wie Sauerstoff, Stickstoff, Schwefel und Phosphor. Es wirkt jedoch hauptsächlich als Kornverfeinerungselement und fördert die Bildung von nadelförmigem Ferrit.
6. Bor, Vanadium und Niob:
Diese Elemente sind für die Kornfeinung im Schweißgut verantwortlich, führen jedoch im Überschuss zur Ausscheidungshärtung.
7. Kalkstein (CaO):
Es ist einer der Hauptbestandteile des Flusses in Bezug auf Lichtbogenstabilität und Fluidität. CaO ist ein sehr stabiles, basisches Oxid. Es verringert die Viskosität und macht das Flussmittel sehr empfindlich gegen Feuchtigkeit. Dieser hygroskopische Charakter führt zu Porosität in der Schweißnaht.
CaO entfernt Schwefel und Phosphor und erhöht die Schlagfestigkeit des Schweißgutes. Es gibt jedoch ein sehr flaches Eindringen und erhöht die Neigung zum Hinterschneiden.
8. Calciumfluorid (CaF 2 ):
Es erhöht die Fließfähigkeit von geschmolzenem Metall und führt zu Sprühübertragung. Es hilft bei der Entfernung von gelöstem Wasserstoff aus geschmolzenem Metallstahl durch Bildung von Fluorwasserstoff, für den Stahl keine Affinität hat.
9. Calciumcarbonat (CaCO 3 ):
Es verringert die Viskosität und macht das Flussmittel basischer. Es vermeidet die Aufnahme von Feuchtigkeit.
10. Desoxidationsmittel (Al, Mn, Ti, Si):
Diese Flussmittelelemente tragen dazu bei, Sauerstoff aus dem Schweißgut zu entfernen, da sie eine höhere Affinität für Sauerstoff haben als andere Elemente. Abgesehen davon verbessern Al, Ti und Mn auch die mechanischen Eigenschaften des Schweißgutes durch Kornfeinung.
11. Natriumoxid (Na 2 O) und Kaliumoxid (K 2 O):
Dies sind Elemente mit niedrigem Ionisierungspotential und sehr instabile Bestandteile eines Flusses. Sie verdampfen und diffundieren in den Lichtbogenhohlraum, wodurch Dämpfe mit geringem Ionisationspotential in der Nähe des Lichtbogens erzeugt werden.
Die Hauptziele der verschiedenen Bestandteile eines Flussmittels sind Lichtbogenstabilität, gewünschte Fließfähigkeit des geschmolzenen Flussmittels und leichte Ablösbarkeit der erstarrten Schlacke nach dem Schweißen.
In Bezug auf die Lichtbogenstabilität beeinträchtigt CaF 2 es, obwohl seine Zugabe zur Kontrolle der Porosität wesentlich ist. Es ist daher unerlässlich, ein Gleichgewicht zwischen diesen widersprüchlichen Anforderungen zu finden. Zu den Elementen, die die Lichtbogenstabilität verbessern, gehören Kalium, Natrium und Calcium. Durch die Beeinflussung der Lichtbogenstabilität wirkt sich die Zusammensetzung eines Flussmittels direkt auf die Formung der Schweißnaht aus.
Eine übermäßige Menge an CaF 2 oder SiO 2 im Flussmittel beeinträchtigt die Lichtbogenstabilität und damit die korrekte Formung der Schweißnaht. Die sich ergebende Schweißnaht ist eng mit übermäßigem Eindringen, da der Lichtbogen kurz wird und weniger manövrierfähig ist. Auf der anderen Seite macht das Vorhandensein einiger Gradienten wie CaO, Na 2 O, K 2 O den Lichtbogen lang und biegsam, und die resultierende Schweißnaht ist breit und weist eine normale Durchdringung auf.
Übermäßige Mengen an CaF 2 und SiO 2 sind auch deshalb unerwünscht, weil sie giftige Fluoride, Kohlenmonoxid (CO) und Stickstoffpentoxid erzeugen, so dass der Inhalt in der Atmosphäre der Schweißerei ständig kontrolliert werden muss.
Die Fließfähigkeit eines Flussmittels im geschmolzenen Zustand ist auch ein Faktor, der die Form einer Schweißnaht beeinflusst. Ein Flussmittel, dessen Fließfähigkeit im geschmolzenen Zustand stark mit der Temperatur variiert, wird als kurzer Fluss bezeichnet, und ein Fluss, dessen Fließfähigkeit mehr oder weniger konstant bleibt, wird als langer Fluss bezeichnet, wie in Fig. 5.2 gezeigt. Lange Flüsse erzeugen grobe Wellen an der Schweißnaht und kurze Flüsse, feine Wellen.
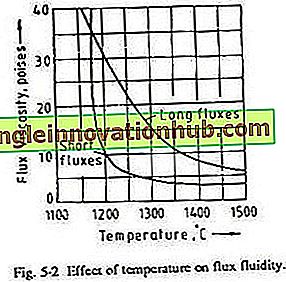
Wenn ein Flussmittel eine geringe Fließfähigkeit für die Erstarrungstemperatur des Schweißmetalls aufweist, ist die Oberfläche der Schweißnaht rau und weist eine Vielzahl von Rippen und Hohlräumen auf. Die Schlacke haftet leicht an einer solchen Oberfläche und ist sehr schwer zu entfernen.
Übermäßige Mengen an SiO 2, MnO und FeO erschweren auch das Ablösen der Schlacke, wodurch die Schweißgeschwindigkeit insbesondere beim Mehrfachschweißen beeinträchtigt wird.
Flüsse sollten auch nicht zu viel Staub bilden, da dies zu Silikose führen kann (einer Lungenerkrankung, die durch eingeblasenen Staub verursacht wird, der Kieselsäure enthält). Als Vorsichtsmaßnahme muss das gesamte Flussmittel mechanisiert werden.
Physikalische Klassifizierung von SAW-Flussmitteln:
Flussmittel für das Unterpulverschweißen werden zu einer kontrollierten Größe granuliert und können eine der zwei Hauptarten sein, nämlich:
(i) geschmolzene Flüsse.
(ii) agglomerierte Flussmittel.
(i) geschmolzene Flussmittel:
Die am häufigsten verwendeten Flüsse sind geschmolzene Flüsse. Sie werden aus Mineralien wie Sand (SiO 2 ), Manganerz (MnSiO 3 ), Dolomit (CaMg (CO 3 ) 2 ) par, Kreide (CaCO 3 ) usw. hergestellt. Wie der Name schon sagt, wird ein geschmolzenes Flussmittel durch Aufschmelzen hergestellt In-Gradienten oben in einem Ofen und nach Bedarf körnig. Es ist frei von Feuchtigkeit und ist nicht hygroskopisch.
Der Grund für das Verschmelzen der Bestandteile besteht darin, dass das Zerquetschen und das mechanische Mischen der Gradienten keine homogene Masse erzeugen. Die Körner der verschiedenen Mineralien unterscheiden sich in der Dichte und sind in der Handhabung voneinander getrennt. Diese Trennung verändert unvermeidlich die Zusammensetzung der Mischung, und das Flussmittel erfüllt nicht seine beabsichtigte Funktion.
Kohlenstoffarme Stähle werden meistens mit Schmelzflussmitteln geschweißt.
Einige der bekannten Schmelzflussmittel sind in zwei Korngrößen erhältlich. Die gröbere Größe ist für automatische Lichtbogenschweißmaschinen und die feinere Größe für halbautomatische tragbare SAW-Maschinen bestimmt. Im ersteren beträgt die Korngröße 3-0 bis 0-355 mm und im letzteren 1-6 bis 0-25 mm. Im Aussehen sind die Körner transparente Teilchen von gelber bis rotbrauner Farbe. Die nominale Zusammensetzung eines dieser Flüsse ist
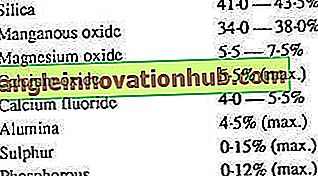
Ein anderes verfügbares Schmelzflussmittel unterscheidet sich auch sehr wenig von dem obigen. Beide werden aus Sand hergestellt, der mindestens 97% Siliciumdioxid enthält, Manganerz, das mindestens 50% Mangan und nicht mehr als 0 bis 2% Phosphor enthält. Flussspat mit 75% CaF 2 und nicht mehr als 0, 2% Schwefel; ätzender Magnesit mit mindestens 87% Magnesiumoxid; und Kohlenstoffträgermaterialien zum Desoxidieren des Flussmittels beim Schmelzen, zum Beispiel Holzkohle, Anthrazit, Koks, Sägemehl usw.
(ii) agglomerierte Flussmittel:
Zu den keramischen Flussmitteln gehören auch die In-Gradienten und das Binden der Körner mit Wasserglas (Natriumsilikat). Diese Flussmittel enthalten Ferrolegierungen (Ferromangan, Ferrosilicium und Ferrotitan) und sorgen für einen hohen Gehalt an Silicium und Mangan und anderen Legierungselementen im Schweißgut.
Ein solches Flussmittel, aus dem alle anderen Klassifizierungen durch Einführen von Legierungszusätzen erhalten werden können, hat folgende Gewichtszusammensetzung:
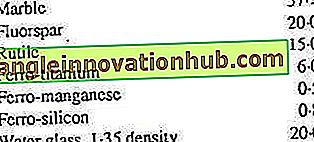
Mit dieser Zusammensetzung kann ein hochlegiertes Schweißmetall mit Elektrodendraht mit niedrigem Kohlenstoffgehalt erhalten werden.
Der Nachteil von keramischen Duxen ist, dass sie leicht Feuchtigkeit aufnehmen und ihre Körner von schlechterer mechanischer Festigkeit sind, weshalb das Flussmittel nicht wiederholt verwendet werden kann.
Keramische Flussmittel sollten in luftdicht verschlossenen Behältern gelagert und vor der Verwendung beansprucht werden. Um Staubbildung zu vermeiden, sollten sie niemals in weichen, wasserfesten Säcken gelagert oder transportiert werden.
Die Faktoren, die die Effizienz eines Flusses zum Erreichen seiner gewünschten Funktionen bestimmen, sind die Tiefe und Breite des Flussbettes sowie die Größe und Form der Flusskörner. Normalerweise sollte das Flussmittelbett mindestens 40 mm tief und 30-40 mm breiter als die Fuge sein. Eine unzureichende Tiefe oder Breite des Flussbettes setzt die Zone der Luft aus, was dazu führt, dass das geschmolzene Metall Stickstoff aufnimmt und die Durchlässigkeit des Schweißgutes verringert wird. Dies gilt auch für grobkörnige Flüsse. Aus demselben Grund sind glasartige Flüsse besser als bimssteinartige.
Beim geschirmten Metall-Lichtbogenschweißen mit stark beschichteten Elektroden wird das Schweißgut mit den in der Beschichtung enthaltenen Ferrolegierungen legiert. Aus diesem Grund kann ein hochlegiertes Schweißmetall sogar mit einem gewöhnlichen Elektrodendraht mit niedrigem Kohlenstoffgehalt erhalten werden. Die am häufigsten verwendeten Schmelzflussmittel enthalten jedoch keine Ferrolegierungen, und die einzigen Legierungselemente sind Silizium und Mangan.
Die Menge an Si und Mn, die das Schweißmetall aufnimmt, hängt von den Schweißbedingungen, der Analyse des Flusses sowie derjenigen der Elektrode und des verwendeten Grundmetalls ab. Die üblichen Zahlen sind 0-1 bis 0-3% Silizium und 0-1 bis 0-4% Mangan.
Der ungefähre Anteil der verschiedenen Hauptbestandteile von Flussmitteln, die von einem großen Hersteller in Großbritannien hergestellt werden, und ihre Auswirkungen auf die Schweißmetallzusammensetzung für einen bestimmten Schweißdraht sind in Tabelle 5.5 aufgeführt.
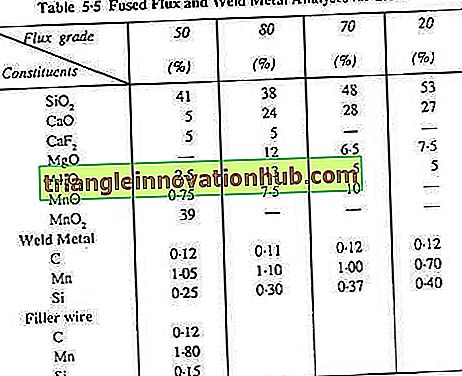
Spezifikation für SAW-Flussmittel:
Gemäß dem AWS-Kodierungssystem werden SAW-Flüsse gemäß den mechanischen Eigenschaften von Schweißgut für einen bestimmten Elektrodendraht spezifiziert.
Der Fluss wird durch ein spezielles Spezifikationssystem identifiziert, das den Präfixbuchstaben F verwendet, um den Fluss zu bezeichnen. Die nächste Ziffer gibt die Mindestzugfestigkeit des Schweißgutes in 10.000 psi (70 N / mm 2 ) an. Die nächste Ziffer oder der nächste Buchstabencode gibt die niedrigste Temperatur an, bei der die Schlagfestigkeit des Schweißgutes 27 J (20 ft-Ib) oder mehr beträgt.
Dieser Code lautet wie folgt:
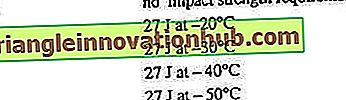
Auf diese Kennziffer folgt ein Bindestrich und dann der Buchstabe E, um eine Elektrode zu kennzeichnen. Es folgt ein Buchstabe, der den Gehalt an Mangan angibt, der L für niedrig (0-30 - 0-60%), M für mittel (0-85 -1-40%) und H für hoch (1-75) ist - 2-25%) Mangan. Darauf folgt eine Zahl, die die durchschnittliche Kohlenstoffmenge in Prozent oder Hundertstel Prozent darstellt.
Zum Beispiel würde F74-EM12 einen SAW-Fluss mit den folgenden Eigenschaften anzeigen:
F - Fluss
7 - Schweißgut mit einer Mindestzugfestigkeit von 500 N / mm 2 (70.000 psi)
4 - Schweißen mit einer Schlagfestigkeit von 27 J bei -40 ° C
E - mit Zusatzdraht als Elektrode
M - Schweißmetall-Mangan mittlerer Konzentration, dh 0-85 bis 1-40%
12 - Schweißkohlenstoffgehalt von 0-12%.
ESW-Flüsse (Elektroschlacke) ähneln SAW-Flüssen, sind jedoch häufiger verschmolzen. „Das Flussmittel muss vollständig in geschmolzenem Zustand bleiben, um Strom zu leiten, damit der ESW-Prozess funktioniert. Das geschmolzene Flussmittel bietet dem Stromfluss den notwendigen Widerstand, um ihn auf der gewünschten Temperatur zu halten.
Das Flussmittel enthält auch Elemente zur Reinigung und Desoxidation des Schweißgutes und schützt es vor den schädlichen Auswirkungen von Luftstickstoff und Sauerstoff. Das Flussmittel im geschmolzenen Zustand muss eine geringere Dichte als Stahl haben, damit es über dem geschmolzenen Metall schwimmt.
Verbrauchsmaterial Nr. 4. Abschirmgase:
Die wichtigsten Schutzgase, die für das Wolframgasschweißen, das Metallgasschweißen und das Plasmaschweißverfahren verwendet werden, sind Argon, Helium und Kohlendioxid. Abgesehen von diesen Stickstoff werden auch Sauerstoff, Wasserstoff und deren Gemische mit den ersten drei Gasen verwendet, um die gewünschte Perlenkonfiguration und Schweißmetalleigenschaften zu erreichen.
Diese Schutzgase lassen sich in zwei Gruppen einteilen:
ein. Inertgase wie (i) Argon und (ii) Helium,
b. Gase, die sich im Metall lösen und damit reagieren, sind beispielsweise CO 2, O 2, H 2 und N 2 .
Argon:
Es ist ein nicht brennbares, nicht explosives Gas, das aus Luft durch Tiefkühlung und Fraktionierung gewonnen wird, wobei es zu 9, 3 x 10 vorhanden ist. Es ist etwa 23% schwerer als Luft.
Im Allgemeinen wird Argon in drei Qualitäten vermarktet, beispielsweise A, B und C, die jeweils 0-01, 0-04, 0-1% Verunreinigungen enthalten. Handelsübliches Argon enthält 16 bis 7% Verunreinigungen. Für erstklassige Schweißarbeiten beträgt die erforderliche Reinheit von Argon etwa 99-995%.
Argon ist nicht toxisch, kann jedoch durch Ersetzen der Luft in geschlossenen Räumen zum Ersticken führen.
Argon wird in standardmäßigen Stahlzylindern in gasförmigem Gefäß gelagert und versandt. Zylinder für reines Argon sind unten schwarz und oben weiß lackiert, auf denen die Worte "Pure Argon" aufgedruckt sind. In einer Flasche wird das Gas unter einem Druck von 150 Atmosphären (ungefähr 15 N / mm 2 ) gehalten - wenn es vollständig gefüllt ist.
Ein 40-Liter-Standardzylinder fasst 6 Kubikmeter (6000 Liter) Argon. Von einem Zylinder wird Argon durch einen am Ventil im Flaschenhals angebrachten Druckregler zum Schweißpunkt geführt. Der Druckregler senkt den Druck des Gases auf den zum Schweißen erforderlichen Wert (der normalerweise unter 0 bis 5 Atmosphären liegt) und hält den Arbeitsdruck unabhängig vom Druck in der Flasche konstant. Die Druckregler für Argonzylinder sind schwarz lackiert.
Die Durchflussmenge von Argon wird mit einem Durchflussmesser gemessen, der als Rotometer bezeichnet wird und an den Regler angeschlossen ist.
Die spezifischen Verwendungen verschiedener Argonqualitäten zum Schweißen sind nachfolgend aufgeführt:
Klasse A:
Argon der Güteklasse A (99-99% oder mehr) wird zum Schweißen aktiver und seltener Metalle sowie zum Schweißen von Bauteilen aus anderen Werkstoffen im Endstadium der Fertigung verwendet.
Note B:
Argon der Güteklasse B (99-96% rein) wird zum Schweißen von Legierungen auf Aluminium- und Magnesiumbasis verwendet.
Note C:
Grad C Argon (99-9% rein) wird zum Schweißen von rostfreien und anderen hochlegierten Stählen verwendet.
Helium:
Helium ist ein seltenes Gas. Es ist nur zu 0-52 x 10-3 % in der Atmosphäre vorhanden. Außerdem ist Helium im Erdgas bis zu 10% vorhanden. Es resultiert auch aus dem Zerfall bestimmter radioaktiver Elemente und wird in einigen Uranmineralien gefunden.
Helium wird aufgrund seiner hohen Kosten vergleichsweise weniger inertes Gas verwendet.
Es ist ein leichtes Gas, das nur 1/7 der Luft wiegt. Dies erschwert den Schutz des Schweißbads und führt zu einem erhöhten Gasverbrauch.
Helium wird in zwei Stufen verkauft. Grad I ist zu 99-6-99-7% rein und Grad II zu 98-5-99-5% rein. Es wird gasförmig in Standardzylindern unter einem Druck von 15 MPa (150 Atome) gelagert und versendet. Handelsübliches Helium I wird in Zylindern aufbewahrt, die braun lackiert sind und keine Inschrift tragen. Handelsübliches Helium II wird in Zylindern aufbewahrt, die braun lackiert sind und das Wort "Helium" tragen, das mit weißer Farbe beschriftet ist.
Helium hat das höchste Ionisationspotential von einem der Schutzgase und daher kann ein Schweißlichtbogen mit einem viel höheren Potential als Argon betrieben werden. Somit erzeugt ein Lichtbogen mit Heliumabschirmung eine größere Wärmemenge. Aufgrund ihres geringen Gewichts neigt Helium dazu, von der Bogenzone weg zu schweben und erzeugt daher eine ineffiziente Abschirmung, sofern nicht höhere Flussraten aufrechterhalten werden.
Sein geringes Gewicht ist jedoch für das Überkopfschweißen hilfreich. Wegen der für Helium erforderlichen höheren Fließgeschwindigkeit sind höhere Schweißgeschwindigkeiten erreichbar. Es ist möglich, mit Helium etwa 35 bis 40% schneller zu schweißen als bei Verwendung von Argon als Schutzgas. Es wird häufig beim Wolfram-Lichtbogenschweißen, beim Metall-Metall-Lichtbogenschweißen und beim automatischen MIG-Schweißverfahren eingesetzt.
Kohlendioxid:
Es ist ein farbloses Gas mit einem leicht wahrnehmbaren Geruch. Wenn es in Wasser aufgelöst wird, ergibt es einen sauren Geschmack. Es ist ungefähr 1, 5 Limetten schwerer als Luft.
Industriell wird CO 2 durch Kalzinieren von Koks oder Anthrazit in speziell entwickelten Kesselfeuerungsräumen und durch Abfangen aus natürlichen Quellen hergestellt. Es wird auch als Nebenprodukt bei der Herstellung von Ammoniak und der Vergärung von Alkohol erhalten
Unter Druck wird CO 2 zu einer Flüssigkeit, die sich bei ausreichender Kühlung zu einer schneeähnlichen Substanz (Trockeneis genannt) verfestigt, die bei -57 ° C verdampft.
Das kommerziell verwendete Trockeneis und gasförmige CO 2 werden aus flüssigem CO 2 erhalten, bei dem es sich um eine farblose Flüssigkeit handelt. Bei Verdampfen bei 0 ° C und Normaldruck (760 mm Hg) erzeugt ein kg CO 2 509 Liter gasförmiges CO 2 .
Flüssiges CO 2 wird in Stahlflaschen transportiert, in denen es 60 bis 80% der Gesamtfläche ausmacht. Ein Standard-40-Liter-Zylinder fasst 25 kg Flüssigkeit, was etwa 15 m3 beträgt. von Gas beim Verdampfen. Der Gasdruck in der Flasche hängt von der Temperatur ab, die sich verringert, wenn mehr Gas aus der Flasche entnommen wird.
Das zum Schweißen verwendete CO 2 kann aus zwei Qualitäten bestehen. Grad I muss mindestens 99-5 Vol .-% reines CO 2 und nicht mehr als 0-178 g / m 3 Feuchtigkeit enthalten. Die entsprechenden Werte für Grad II betragen 99-0% und 0-515 g / m 3 .
Die Durchdringungseigenschaften von CO 2 sind aufgrund von Gewichtsähnlichkeiten der Gase ähnlich den Durchdringungseigenschaften von Helium. CO 2, das zum Schweißen verwendet wird, muss frei von Feuchtigkeit sein, da Feuchtigkeit Wasserstoff freisetzt, der im Schweißgut Porosität erzeugt. Da CO 2 einen höheren elektrischen Widerstand hat, muss die Stromeinstellung 20 bis 30% höher sein als bei Argon und Helium.
Bei normaler Temperatur und normalem Druck gilt CO 2 als inert. Bei erhöhten Temperaturen dissoziiert es jedoch zu 20 bis 30% in CO und O. CO ist toxisch und hat eine sichere Konzentration von nur 175 ppm (parts per million) im Vergleich zu 5000 ppm für CO 2 . Dies erfordert ein wirksames Abgassystem, um die schädlichen Auswirkungen von CO zu schützen.
Die negative Eigenschaft der Sauerstoffbildung ist, dass sie die Nennfestigkeit des Metalls verringern kann. Ein weiterer großer Nachteil des Einsatzes von CO 2 ist seine extreme Beständigkeit gegen Stromfluss. Aufgrund dieses Widerstands ist die Bogenlänge empfindlich. Wenn die Bogenlänge zu lang ist, erlischt sie leichter als bei Verwendung eines Inertgases wie Argon oder Helium.
Defekte Schweißnähte werden meistens erzeugt, wenn CO 2 vom oberen oder unteren Teil eines Zylinders verwendet wird. Dies liegt daran, dass das Gas an der Spitze die meisten Verunreinigungen (Stickstoff, Sauerstoff und Feuchtigkeit) trägt, während dessen Wasser vorhanden sein kann. 150-200 g / Zylinder sammelt sich unter dem flüssigen CO 2 am Boden. Wenn das flüssige CO 2 vollständig aufgebraucht ist, enthält das aus der Flasche austretende Gas zu viel Feuchtigkeit.
Um Defekte durch Verunreinigungen in CO 2 zu vermeiden, ist es ein guter Plan, das frisch gelieferte CO 2 für 15, 20 Minuten absetzen zu lassen und den oberen Teil des Inhalts in die Atmosphäre abzugeben. Es ist auch eine gute Praxis, einen Zylinder auf den Kopf zu stellen und etwa 15 Minuten in dieser Position ruhen zu lassen. Nach dieser Zeit das Ventil vorsichtig öffnen, das gesamte Wasser im Zylinder fließt ab.
Wenn CO 2 mit einer Geschwindigkeit von über 1000 Litern / Stunde (bei kontinuierlichen Schweißvorgängen) angezapft wird, ist es für einen Bediener ratsam, mindestens zwei parallel geschaltete Zylinder zu verwenden.
Wenn große Mengen an CO 2 beteiligt sind, kann es in Tankwagen verschifft und in Verdampfer gefüllt werden. CO 2 kann auch als Trockeneis verschickt und beim Anwender verdampft werden. Die Verwendung von festem CO 2 zum Schweißen bietet wesentliche Vorteile durch die hohe Reinheit des Gases und eine bessere Transportfähigkeit. Briketts aus festem CO 2, wie sie von einem Lieferanten geliefert werden, werden in speziellen Behältern, die entweder mit Strom oder mit heißem Wasser beheizt werden, in Gas umgewandelt.
Andere Gase:
Im Allgemeinen werden Ar, He und CO 2 einzeln oder in Mischungen als Schutzgase zum Schweißen verwendet. Häufig werden diesen Gasen jedoch andere Gase wie O 2, H 2 und N 2 zugesetzt, um bestimmte gewünschte Formen und Eigenschaften der Schweißnähte zu erreichen.
Sauerstoff ist ein farbloses, geruchloses und geschmackloses Aktivgas, das sich mit vielen Elementen zu Oxiden verbindet. In Stahl kann es sich mit Kohlenstoff verbinden, um CO zu bilden, das sich im erstarrenden Schweißgut verfangen und zu Poren oder Hohlräumen führen kann. Dieser Mangel wird normalerweise durch die Zugabe von Desoxidationsmitteln wie Mn und Si überwunden.
Wasserstoff ist das leichteste Gas, das zu 0 - 01% in der Atmosphäre vorhanden ist. Wasserstoff kann jedoch auch in der Lichtbogenatmosphäre aus Feuchtigkeit oder Kohlenwasserstoffen vorhanden sein, die auf dem Grundmetall oder dem Fülldraht vorhanden sind. Es löst sich in geschmolzenem Stahl auf, aber seine Löslichkeit in Stahl ist bei Raumtemperatur sehr gering. Somit gelangt der austretende Wasserstoff an die Korngrenzen und kann zu Rissen führen. Dies verursacht auch eine Wulstfraktion in der HAZ.
Stickstoff ist reichlich in der Atmosphäre. Es ist farblos, geruchlos, ungiftig und fast ein Inertgas. Es ist in geschmolzenem Stahl löslich, aber seine Löslichkeit in Stahl bei Raumtemperatur ist sehr gering. Somit können auch Poren und Fehlstellen entstehen. In sehr kleinen Mengen können Nitrite, wenn sie gebildet werden, die Festigkeit und Härte von Stahl erhöhen, jedoch seine Duktilität verringern, was zu Rissbildung führen kann. Manchmal wird zum Schweißen von Kupfer Stickstoff verwendet, da er einen hohen Wärmelichtbogen erzeugt. Aufgrund seiner geringen Kosten im Vergleich zu Argon wird es häufig zum Spülen von Edelstahlrohr- und Rohrsystemen verwendet.
Gasgemische:
Gasgemische, die üblicherweise in Lichtbogenschweißverfahren eingesetzt werden, umfassen Ar-He, Ar-CO 2, Ar-O 2, Ar-H 2, Ar-CO 2 -O 2 und dergleichen.
Verhältnis von Argon in Ar-He-Gemischen kann von 25 bis 95% Ar variieren. Beim Schweißen von Aluminium wird jedoch häufig eine Mischung aus Ar-75% He oder Ar-80% He verwendet. Argon als Schutzgas hilft bei der Entfernung von Oxiden und zeigt auch eine gewisse Kontrolle der Porosität der Schweißnaht. Helium hilft dabei, eine gute Perlenkonfiguration zu erhalten. Die meisten Eisen- und Nichteisenmetalle können entweder mit Helium oder Argon oder deren Gemischen verschweißt werden. Helium eignet sich besonders zum Schweißen von schwereren Abschnitten aus Aluminium, Magnesium und Kupfer sowie zum Überkopfschweißen.
Eine Mischung aus CO 2 - 75% Ar oder CO, -SO 2 % Ar ist beim Schweißen von Baustählen und niedriglegierten Stählen sehr beliebt. Argon verbessert die Metallübertragungseigenschaften, und CO 2 hilft bei der Verbesserung der Perlenform und der Wirtschaftlichkeit des Prozesses. Diese Mischungen werden jedoch bei dünneren Abschnitten von Stählen verwendet, wenn das Aussehen der Raupen wichtig ist. Diese sind auch für das Schweißen außerhalb der Position bei extrem dünnen Blechen nützlich.
Manchmal wird Argon Sauerstoff zugesetzt, um die Wulstform beim Schweißen von Stählen mit niedrigem Kohlenstoffgehalt zu verbessern. Eine geringe Menge an Sauerstoff, die Argon zugesetzt wird, führt zu signifikanten Veränderungen. Zum Beispiel verbreitert es den tiefen Eindringfinger in der Mitte der Perle; Es verbessert auch die Wulstkontur und beseitigt die Hinterschneidung am Rand der Schweißnaht.
Sauerstoff wird normalerweise in Mengen von 1%, 2% oder 5% zugesetzt. Die maximale Menge an Sauerstoff, die für Ar-O 2 -Mischungen verwendet wird, beträgt 5%. Wenn höhere Mengen hinzugefügt werden, kann dies zu Porosität im Schweißgut führen. Das Hauptziel der Zugabe von Sauerstoff zu Argon besteht darin, auf der Oberfläche der Stahlelektrode thermionisches Eisenoxid zu bilden, das sein Emissionsvermögen verbessert und den Kathodenfleck breiter und stabiler macht, wenn die Elektrode negativ gemacht wird.
Argon wird manchmal mit Wasserstoff versetzt, seine Menge ist jedoch auf maximal 5% begrenzt. Normalerweise werden als Gemische Ar-2% II oder Ar-4% H 2 verwendet . Die Zugabe von Wasserstoff führt zu einer Erhöhung der Lichtbogenspannung, was zu einer höheren Wärmeentwicklung im Lichtbogen führt. Die Ar-H 2 -Mischung sollte nicht für kohlenstoffarme oder niedriglegierte Stähle verwendet werden, da dies zu Wasserstoffbrüchen führen kann, die häufig als Wasserstoffversprödung bezeichnet werden. Es wird hauptsächlich zum Schweißen von Nickel oder Ni-Legierungen verwendet. Mit dieser Mischung werden auch schwere Profile aus nichtrostenden Stählen geschweißt.
Zum Schweißen von Baustählen wird manchmal auch eine Mischung aus CO 2 - O 2 oder Ar-CO 2 - O 2 verwendet. Dies verbessert die Art der Metallübertragung und der Wulstform. Die Zugabe von Sauerstoff führt zu einem heißeren Laufen des Lichtbogens und vermeidet so den Mangel an Fusion.
Die Verwendung von Chlor in geringen Mengen als Schutzgas für Aluminium verbessert die Lichtbogenstabilität. Auch Stickoxid als sehr geringer Zusatz (<0–03%) zum Schutzgas zum Schweißen von Aluminium trägt dazu bei, den Ozongehalt in der Schweißzone zu reduzieren.
Im Allgemeinen kann die Zusammensetzung des Schutzgases für das Schutzgasschweißen verschiedener Metalle und ihrer Legierungen auf den in Tabelle 5.6 angegebenen Richtlinien basieren. Mit verschiedenen Schutzgasen erhaltene Perlenformen sind in Abb. 5.3 dargestellt.

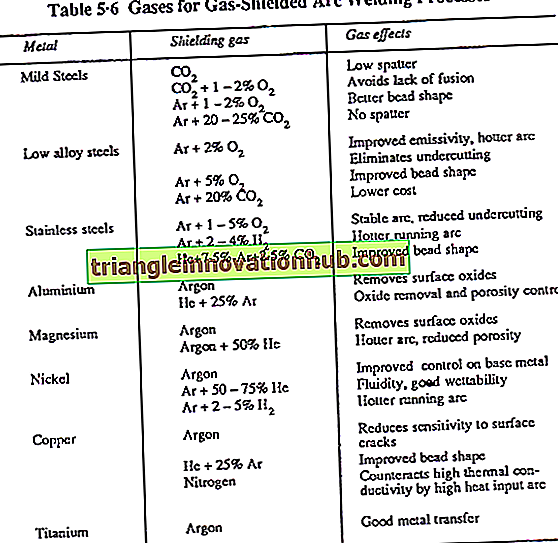